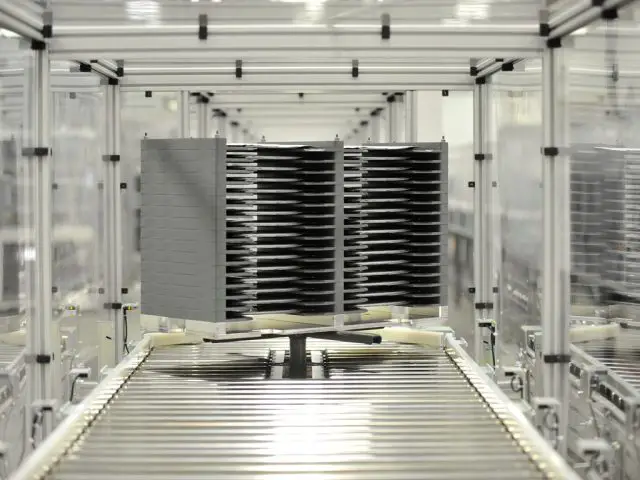
Kijkje in de keuken: fabricage van batterijen bij Nissan
Wereldwijd hebben de berijders van de Nissan Leaf een miljard kilometers afgelegd met hun volledig elektrisch aangedreven auto. Ter ere van die mijlpaal opende Nissan eenmalig voor een select gezelschap de deuren van zijn batterijfabriek in het Engelse Sunderland. Daarmee gunde de fabrikant ons een exclusief kijkje in de keuken.
Nissans fabriek in Sunderland is de enige fabriek ter wereld waarin batterij- en autoproductie onder één dak plaatsvinden. Hoewel Nissan nu een blik gunt in de fabriek, geven ze niet alles prijs: “We laten jullie zien hoe we de taart bakken, maar niet welke ingrediënten we erin doen”, grapt Jim Wilkinson, productiemanager in de fabriek.
Stofvrij
De fabriek verzorgt de batterijproductie van A tot Z. Dat gebeurt voor een groot deel in een zogenoemde ‘Clean Room’: een grote ruimte met een droge en stofvrije atmosfeer. “De Clean Room in Sunderland is een van de grootste in Europa, dan wel dé grootste”, vertelt Wilkinson.
Voordat je de Clean Room mag betreden, moet je een speciaal stofvrij pak aan, inclusief mondkapje en speciale (hand)schoenen. En vervolgens moet je door een luchtsluis met een luchtdouche, om de laatste stofdeeltjes te verwijderen.
“Het lijkt overdreven, maar mensen zijn de grootste ‘vervuilers’ van de Clean Room”, aldus Wilkinson. “Stof en ander vuil is funest voor de batterijproductie, want het kan kortsluiting veroorzaken in de batterij.”
Kwaliteit
“De vereiste kwaliteit van de batterij is een van de belangrijkste redenen waarom we de batterijproductie in eigen hand houden. Alleen dan kunnen we de kwaliteit garanderen”, aldus Jean-Pierre Diernaz, Director of Electric Vehicles bij Nissan Europa. Tijdens de productie vinden dan ook veel strenge controles plaats. Bijvoorbeeld de toleranties van zowel de batterijen als het gereedschap; die worden gemeten in micrometers. De gehele productie kent in totaal zo’n tweeduizend kwaliteitscontroles.
“We bouwen de batterij op uit modules, die weer bestaan uit cellen. Uiteindelijk worden de cellen onder hoogspanning getest. Als er stof of vuil in de cel zit, ontstaat er kortsluiting. Als dat niet gebeurt, weten we dat de cel goed is”, aldus Wilkinson.
Naar de productielijn
In de Clean Room worden de cellen geproduceerd. In een andere ruimte plaatsen medewerkers de cellen in een module. Als laatste monteren ze die modules in een batterij.
Een deel van de batterijen wordt vervoerd naar de Nissan-fabriek in Barcelona, voor de productie van de eNV-200. Het andere deel wordt gebruikt op de Leaf-productielijn in Sunderland. “Zo bijzonder als de productie van de batterij is, zo gewoon is de productie van de Leaf. De elektrisch aangedreven auto wordt op dezelfde productielijn in elkaar gezet als de Qashqai, de Juke en de Note. Eén verschil: de Qashqai wordt voorzien van een brandstoftank en de Leaf van een batterij”, vertelt de gids in de fabriek.
Bekijk ook de korte video van de productie:
Nog geen reacties