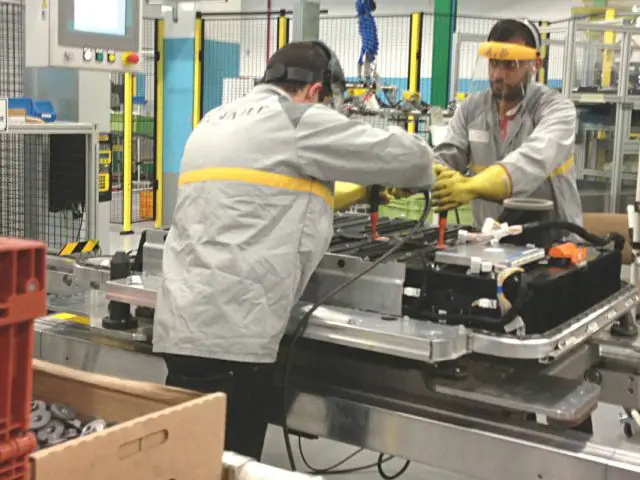
Gluren achter de deuren van een EV-fabriek
De Franse zon schijnt verblindend wit licht neer op de autofabriek. In de productiehallen is het licht gedempt en ook de temperatuur is er aangenaam. De lucht ruikt naar ijzer. Ondanks de voortdurende malende transportbanden en ritmisch zwaaien van de robotarmen is het er rustig. Schijn bedriegt: met honderdeden per dag worden hier Renaults Clio en Zoe gebouwd. Van de nieuwe elektrische Renault rolde onlangs het 5.000e exemplaar van de band. ZERauto kijkt achter de schermen bij 550 robots en 2.800 medewerkers.
Soft revoltion
De Renault-fabriek in Flins, naast Parijs, is meer dan zestig jaar oud. Althans, de plek – de fabriek zelf is als een organisme dat met de tijd meegroeit en verandert. Ook nu. Tijdens een ‘soft revolution’ is Usine de Flins na 17 miljoen gebouwde auto’s opnieuw aangepast aan de toekomst.
De Renault Zoe en Clio delen dezelfde productielijn. Dat is op zich niet zo gek: het zijn allebei compacte hatchbacks met voorwielaandrijving. Er zijn meer overeenkomsten dan verschillen tussen de twee modellen. Met een klein beetje fantasie kun je je voorstellen dat de elektrische Zoe van de tekentafel kwam als ontwerpvoorstel voor de nieuwe Clio-generatie.
50 tot 80 per dag
In de fabriekshallen domineren de Clio’s de productielijnen – hier en daar afgewisseld door een Zoe. In 2012 bedroeg de productie 116.000 auto’s waarvan 446 Zoe’s. Dagelijks maakt de fabriek 40 tot 80 exemplaren, afhankelijk van de vraag.
Thierry Chravat, directeur van de Clio- en Zoe-fabriek: ‘We leveren de Zoe nu in 11 landen in West-Europa. We hebben 6.000 orders, waarvan 5.000 zijn uitgeleverd. Op onze productielijn lopen 3 modellen door elkaar: de nieuwe Clio, de Zoe en de Clio Collection, de vorige generatie Clio. De productiestart van de Zoe is een ‘soft revolution’. De opzet van de productielijn bleef onveranderd en met maar een paar aanpassingen konden we de Zoe aan de lijn toevoegen.’
Om de elektrische Zoe in de productielijn op te nemen heeft een team van 350 mensen de stap achter de schermen voorbereid. Daarnaast volgden er 50.000 trainingsuren aan de medewerkers en bouwde de mensen 250 proefauto’s.
4.390 puntlassen
Op maar enkele plekken is de productielijn aangepast: bij de persstraat waar het plaatwerk wordt gemaakt en bij de assemblagelijn voor het monteren van de accu. Daarnaast werden nieuwe lakkleuren aan de spuitstraat toegevoegd. Van de 550 robots werden 150 exemplaren vervangen door een model dat meer verschillende handelingen kan verrichten. Voor de Zoe zijn bijvoorbeeld 4.390 puntlassen nodig, 400 meer dan voor de Clio. Ongeveer 40 robots werken uitsluitend aan de Zoe-productie, bijvoorbeeld voor de assemblage van de accu.
Accuproductie
Voor de productie van de accu is een complete montagehal van 500 vierkante meter opnieuw ingericht. Uit Zuid-Korea arriveren hier de accumodules van LG. In elke accu zitten 12 van deze 17 kilo wegende modules. Samen met de regelelektronica worden ze in een water- en luchtdichte behuizing geplaatst. Nadat ze handmatig zijn geactiveerd (400 Volt) brengt een zelfrijdende trolley ze naar een opslagruimte. Vandaar worden ze – opnieuw zonder mensenhanden – naar de productielijn gebracht. Een kleine hydraulische lift zorgt dat de accu tegen de onderzijde van de bodem wordt geplaatst, waarna ze bouten bevestigd worden. Aan de assemblage van de accu werken 8 mensen die zo’n 100 accu’s per dag kunnen bouwen.
[ytvideo id=”1″]
Meer over de Renault Zoe
1e kennismaking met de Renault Zoe
De EV-ervaringen van Zoe-rijder Frank Buschmam
Nog geen reacties